Vom Granulat zum Schutzblech
Das perfekte Produkt in 8 Schritten
Hast du dich schon einmal gefragt, wie ein Schutzblech entsteht? Durchdachte Entwicklungen und modernste Technik sind nötig, um das perfekte Produkt herzustellen. Begleite uns Schritt für Schritt durch den Fertigungsprozess des MUDROCKERS! Wir versprechen dir: Es ist ziemlich spannend.
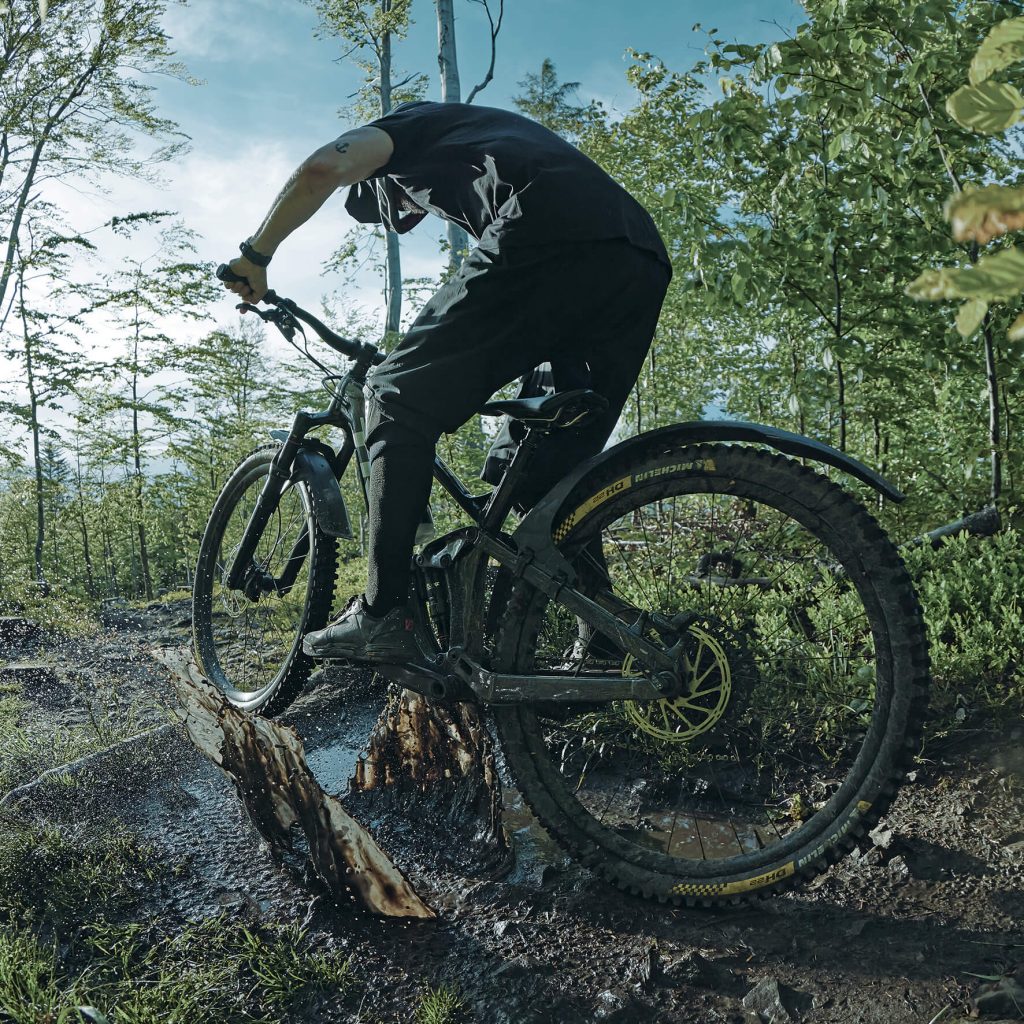
Schritt 1: Am Anfang steht die Idee
Was ist gerade Trend? Welche neuen Fahrrad-Geometrien gibt es? Unsere Produktmanager haben die Bike-Branche ständig im Blick. Nach einer umfassenden Marktanalyse entsteht schließlich die Produkt-Idee. Neben der Benutzerfreundlichkeit und Sicherheit des Produkts ist es wichtig, dass alle Komponenten wirtschaftlich und qualitativ hochwertig produziert werden können.
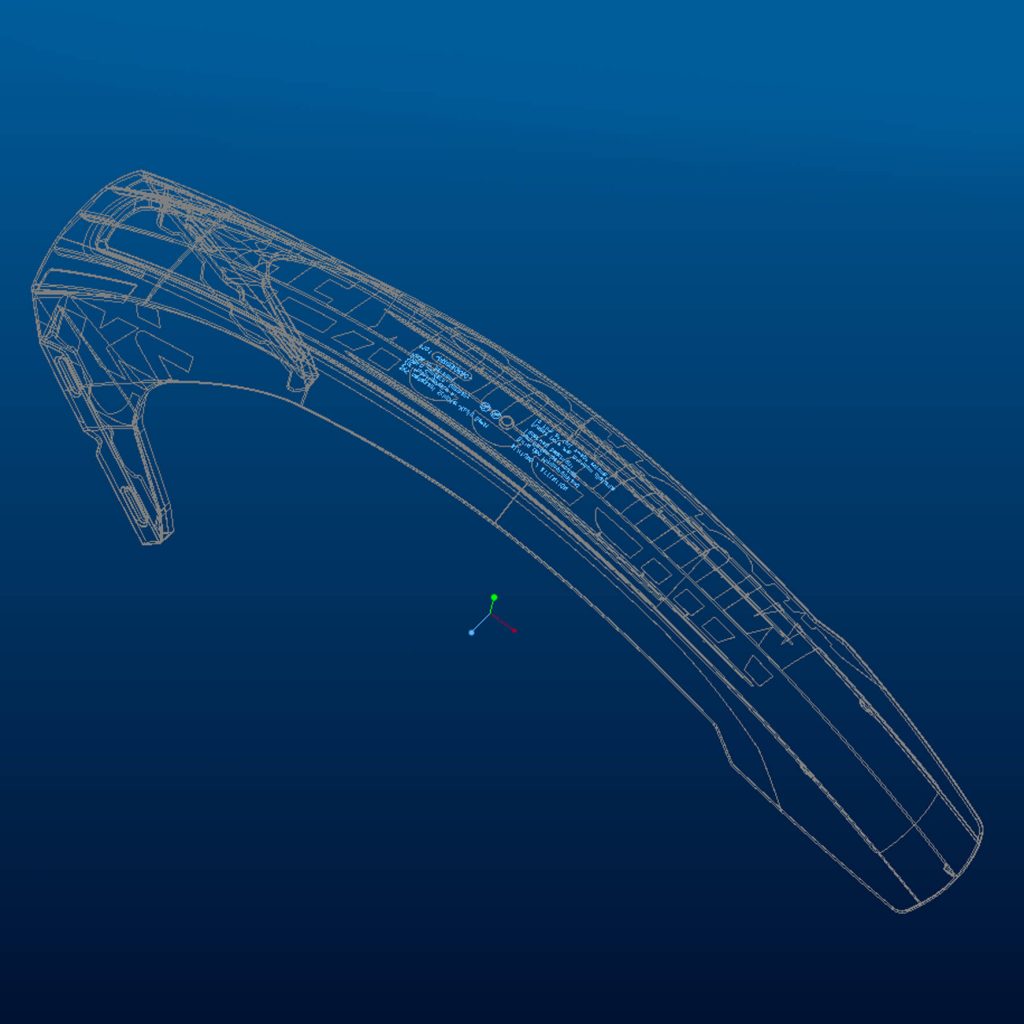
Schritt 2: Das Baby nimmt Formen an
Alle Projektteilnehmer aus dem Produktmanagement, der Entwicklung und Konstruktion sowie aus dem Werkzeugbau arbeiten „inhouse“ und sind bestens miteinander vernetzt. Als erstes ist die Entwicklungsabteilung am Zug: Das Schutzblech wird zunächst rein technisch in 3D am Computer konstruiert und anhand der Daten wird ein Prototyp auf dem 3D-Drucker erstellt.
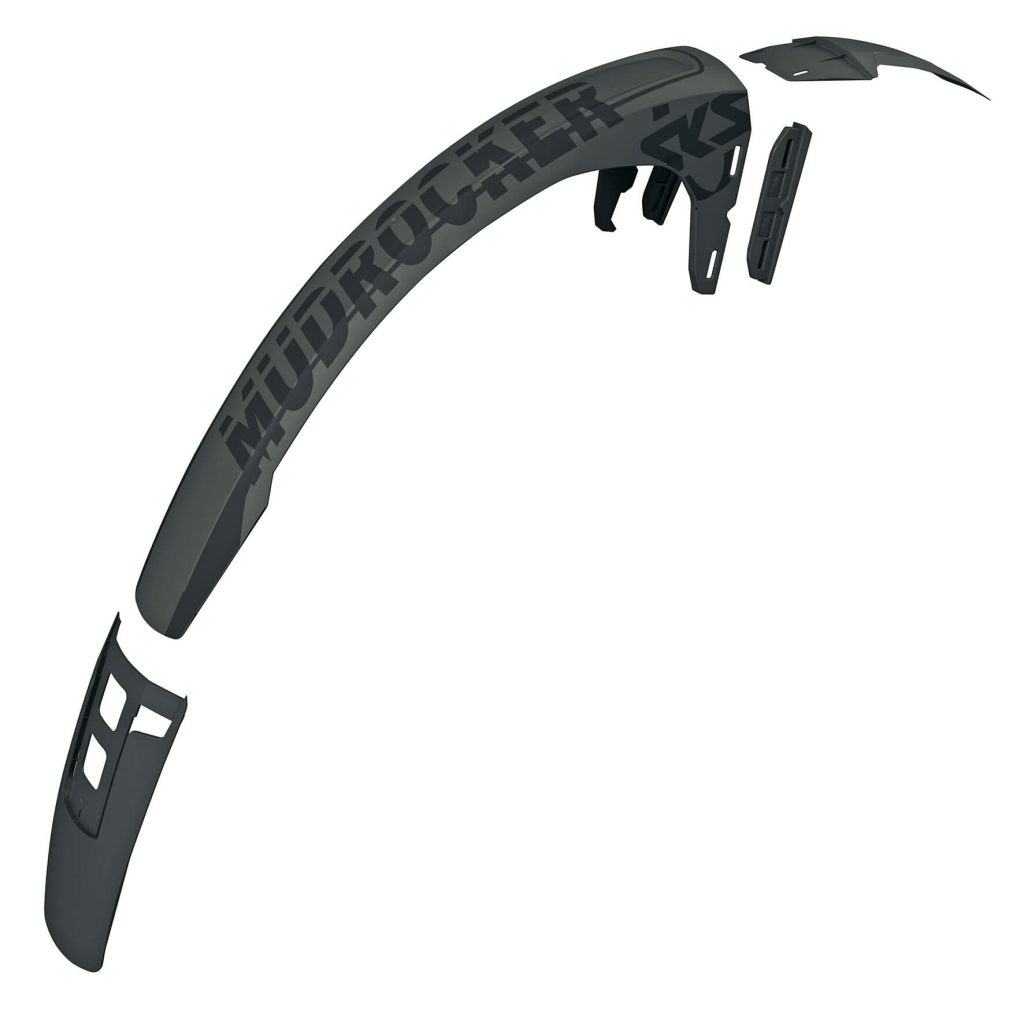
Schritt 3: Testen, testen, testen
Unser Team ist sehr fahrradaffin. Deshalb wird der Prototyp von SKS-Kolleginnen und Kollegen bei Feldversuchen auf Herz und Nieren geprüft. Auch unsere „Wasserspritzmaschine“ bietet aufschlussreiche Erkenntnisse: Das mit den Prototypen ausgestattete Fahrrad rollt auf einem nassen Laufband, um eine Fahrt bei Regen zu simulieren. Nun wird genau analysiert, welchen Schutz der Prototyp bietet.
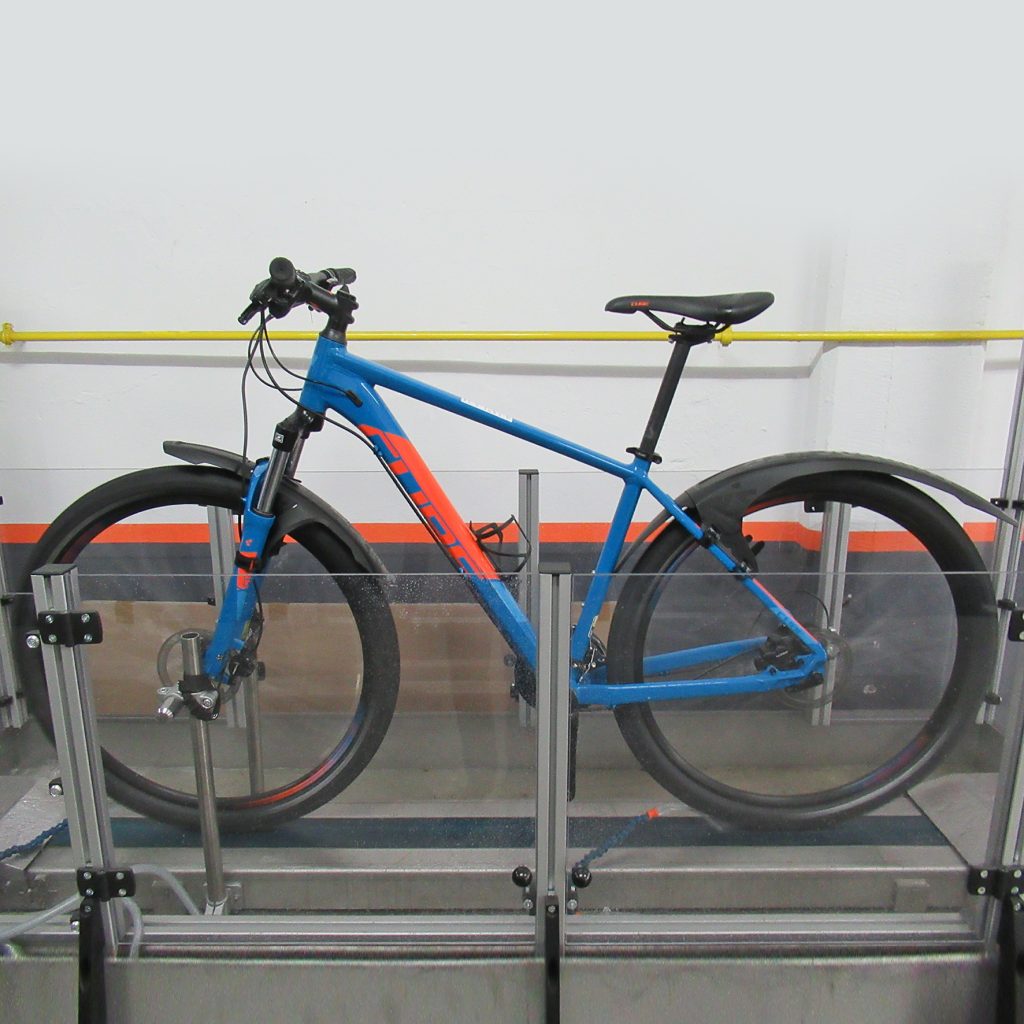
Schritt 4: Maßgeschneidertes Design
Natürlich soll ein Schutzblech nicht nur praktisch sein, sondern auch gut aussehen. Daher starten nun unsere Designer, um die technische Konstruktion mit einer ansprechenden, modernen Optik auszustatten. Ein weiterer Prototyp mit dem finalen Design entsteht und wird von unseren Experten im Detail überprüft. Wenn nun alles perfekt ist, werden die Spritzgussformen im 3D-Verfahren konstruiert.
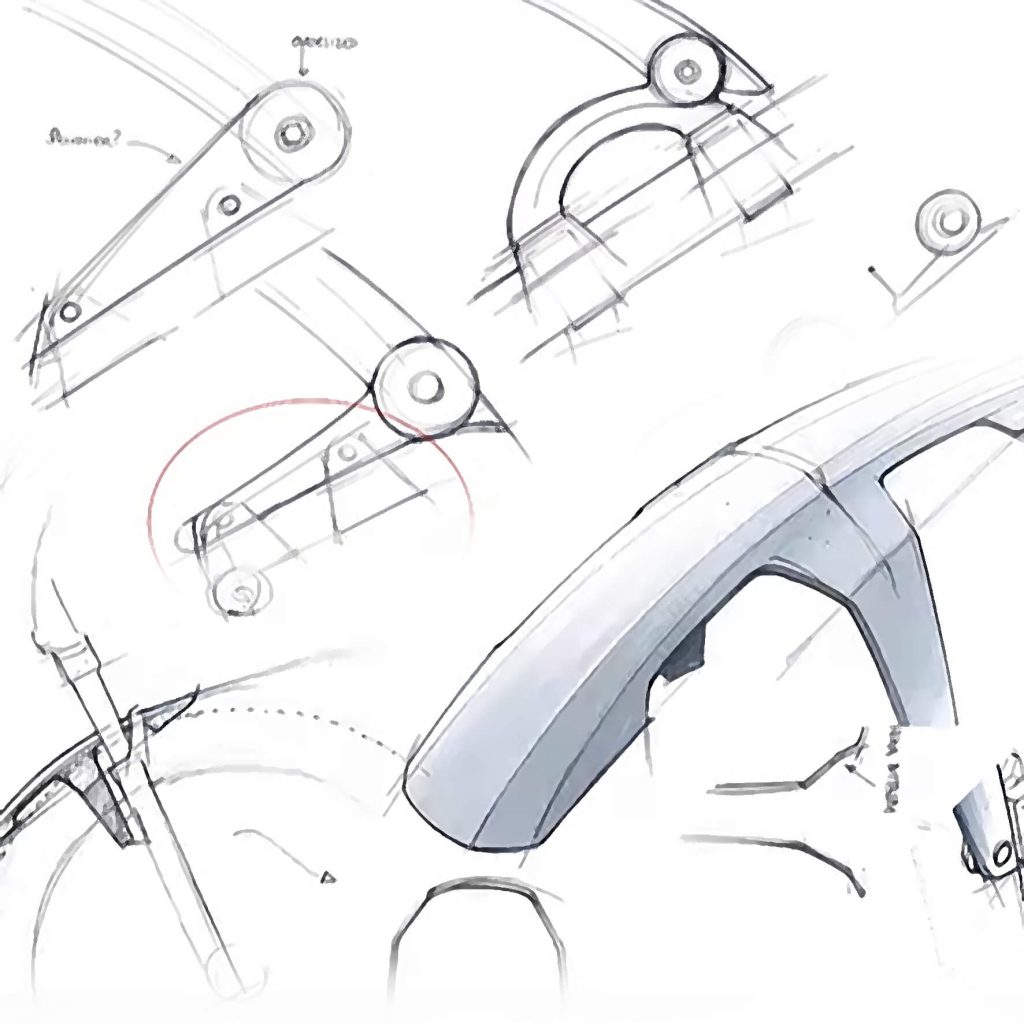
Schritt 5: Jetzt ist Millimeterarbeit gefragt
Auf hundertstel Millimeter genau werden die Spritzgussformen nun im eigenen Werkzeugbau gebaut. Die Form besteht aus zwei Hälften, nämlich der Düsenseite und der Auswerferseite. Tagtäglich arbeiten 15 Werkzeugmechaniker an neuen Werkzeugen. Rund 2000 Spritzgusswerkzeuge sind für die Produktion von Fahrradzubehör bei SKS bereits gefertigt worden.
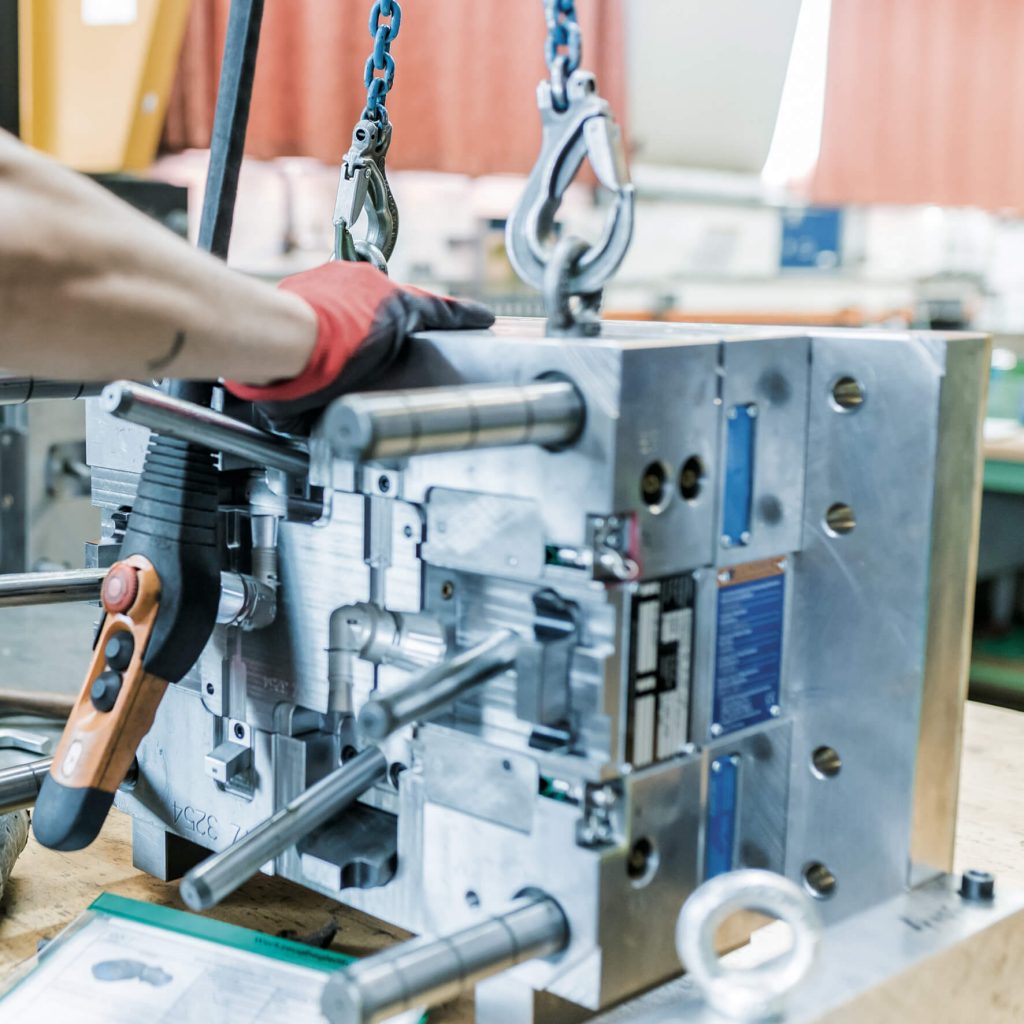
Schritt 6: Recycelbarer Rohstoff
Das Kunststoffgranulat lagert u. a. in großen Silos auf dem SKS-Gelände. Wir verwenden thermoplastische Kunststoffe, die eingeschmolzen und neu geformt werden können. Durch mechanisches Zerkleinern lassen sich die Kunststoffe energiesparend vollständig recyceln. Das Recycling-Granulat kann anschließend als Rohstoff für die Herstellung neuer Produkte eingesetzt werden.

Schritt 7: Unter Druck
Vom Silo gelangt das Granulat durch ein Rohrleitungssystem zu einer der 75 Spritzgussmaschinen. Wie in einem Fleischwolf wird der Kunststoff nun durch eine Förderschnecke gedreht, erhitzt und homogenisiert. Unter Druck wird die heiße Kunststoffmasse in die zuvor eingebaute Spritzgussform gespritzt, wo sie aushärtet und anschließend als fertiges Schutzblech aus der Hohlform geworfen wird.
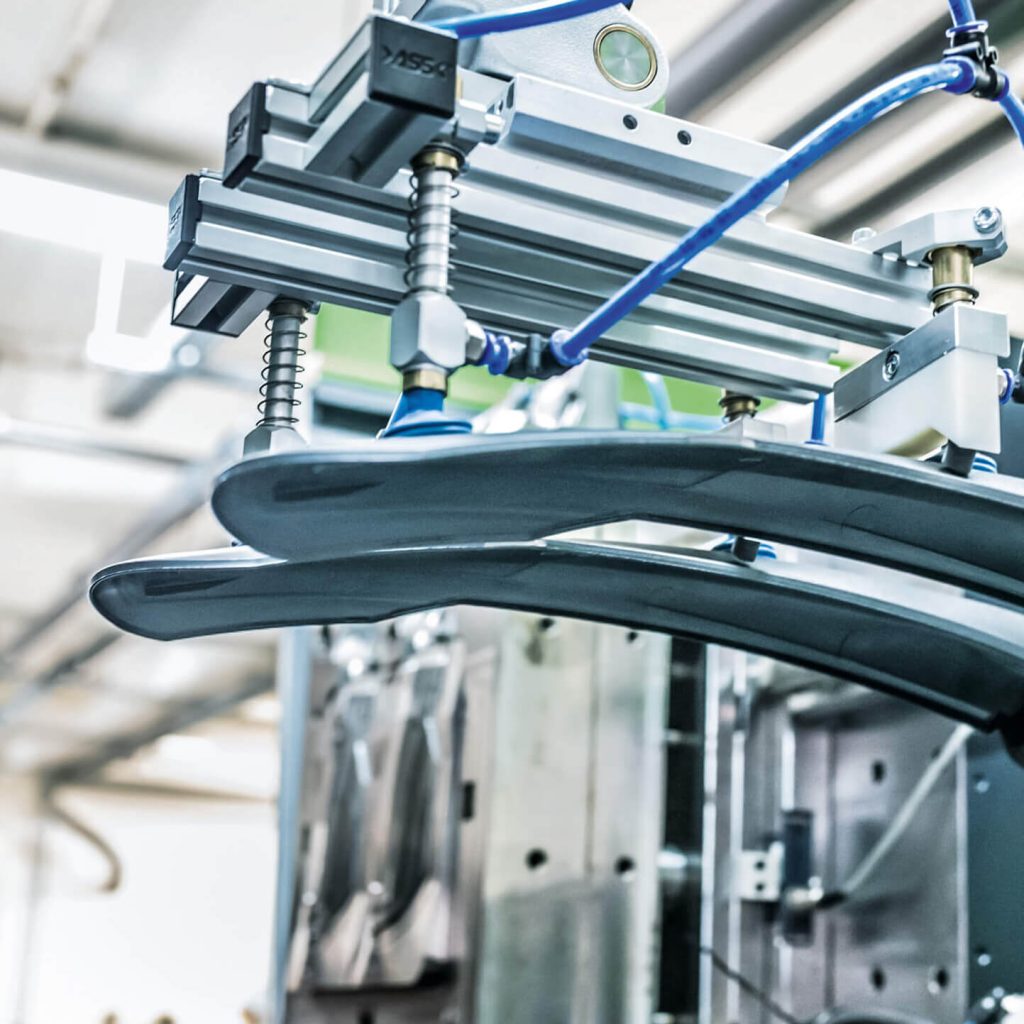
Schritt 8: Ab in die Welt
Nach der Qualitätsprüfung werden die MUDROCKER verpackt und sind bereit, um in die Welt verschickt zu werden. Vielleicht entdeckst du beim Fahrradhändler demnächst ein Schutzblech von SKS GERMANY. Dann weißt du jetzt, mit wieviel Sorgfalt es entstanden ist. Und dass seine langlebige Qualität dazu beiträgt, Ressourcen und somit die Umwelt zu schonen. Made in Germany – made with love!
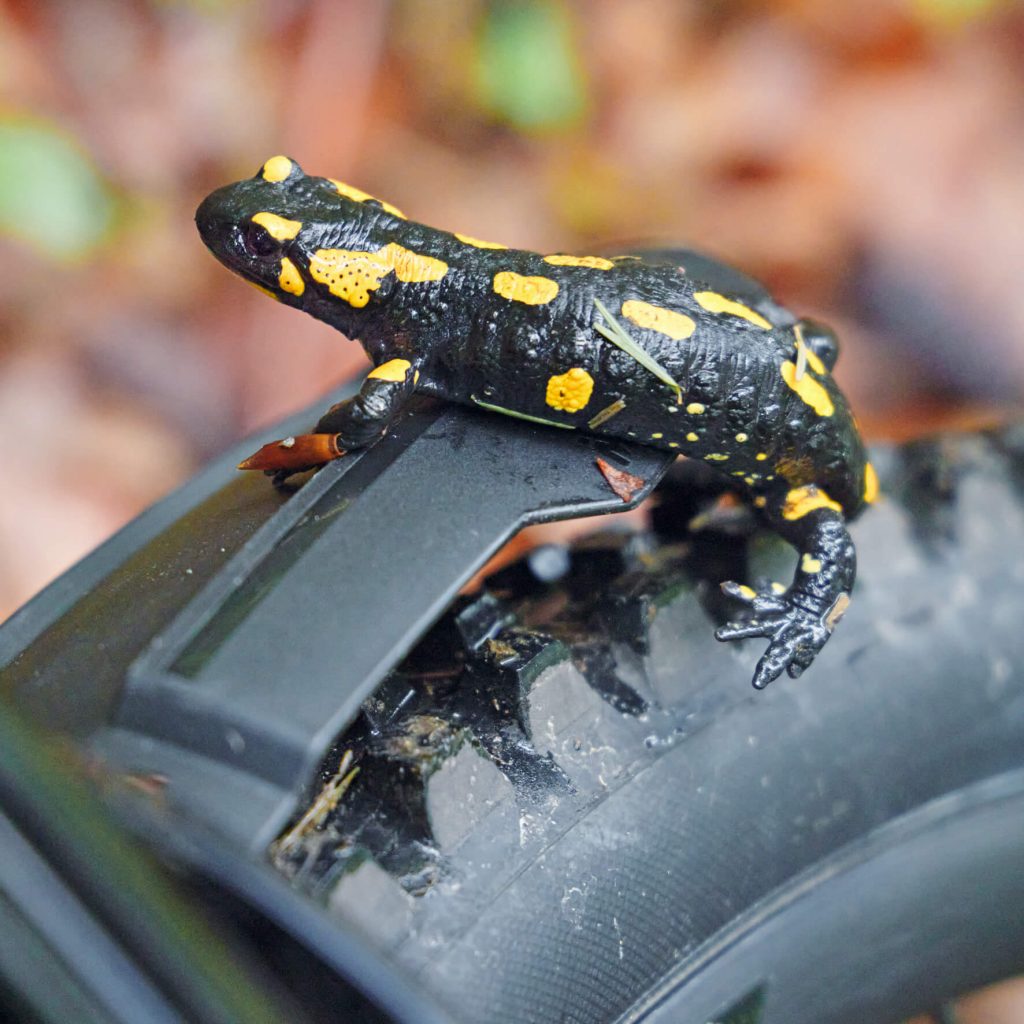